Choosing the Right Coating: A Guide for Your Project
- Charles McCarthy
- Jan 1, 2024
- 2 min read
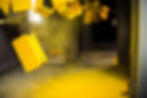
Selecting the appropriate finishing method is crucial for ensuring the longevity, durability, and aesthetic appeal of Your project. The various options available at MFAB are: Kynar, powder coating, paint, and hot-dip galvanizing Each method comes with its own set of advantages and disadvantages, catering to different needs and environments. This list is designed to help guide you in the direction but if you have any additional questions feel free to discuss your options with our team and we will do our best to guide you in the right direction.
Kynar Coating:
Exceptional durability: Kynar coatings are known for their resistance to UV radiation, chemicals, and harsh weather conditions, ensuring long-lasting protection.
Vibrant color options: Kynar coatings offer an extensive range of color choices, allowing for customization to meet specific design requirements.
Low maintenance: The self-cleaning properties of Kynar coatings make them relatively low maintenance, reducing the need for frequent cleaning or touch-ups.
Cons:
Cost: Kynar coatings are very expensive compared to other finishing options, which can impact overall project budgets.
Kynar is softer than other coatings and is prone to scratching.
Powder Coating:
Wide color variety: Powder coating provides an extensive color palette with a smooth and even finish.
Excellent durability: Powder-coated surfaces are resistant to chipping, scratching, and fading, ensuring a long lifespan.
Environmentally friendly: Powder coating is a more environmentally friendly option, as it produces less waste and uses no volatile organic compounds (VOCs).
Cons:
Limited thickness options: Achieving a thicker coating with powder coating can be challenging, affecting the level of protection in some applications.
Repair can be difficult if damaged
Paint:
Cost-effective: Paint is generally more cost-effective than some other finishing methods, making it a practical choice for budget-conscious projects.
Easy application: Painting is a straightforward process that can be applied with brushes, rollers, or sprayers, offering flexibility in application.
Cons:
Prone to chipping and fading: Painted surfaces may be more susceptible to chipping, scratching, and fading over time, especially in harsh environmental conditions.
Limited lifespan: The longevity of painted surfaces may be shorter compared to other finishing options.
Hot-Dip Galvanizing:
Superior corrosion resistance: Hot-dip galvanizing provides excellent protection against corrosion, making it ideal for outdoor and industrial applications.
Long lifespan: Galvanized coatings have a long life expectancy, requiring minimal maintenance over time.
Self-healing properties: The zinc coating in hot-dip galvanizing can naturally repair minor damages, extending the life of the coating.
Coating of the interior of the parts.
Cons:
Hot-dip galvanizing results in a silver or gray appearance.
Parts that are going to be hot dip galvanized after fabrication require specific design features in order to prevent hot gasses from expanding in sealed components and exploding.