Welding Certifications: Its Complicated...
- Charles McCarthy
- Jun 21, 2024
- 4 min read
Updated: Jul 23, 2024
Understanding the Term "Certified Welder" and Its Implications for Your Project
When you're looking to hire a welding shop for your project or are working with MFAB, it is common to ask the shop if their welders are "certified." While this seems like a straightforward question, the term "certified welder" is actually quite broad and can be misleading if not properly understood. In this post I am going to attempt to give as simple an explanation into what it means for a welder to be certified, the different types of certifications available, and why it's crucial to be specific about your project requirements when inquiring about certifications. This is just the broad strokes and not intended to be a comprehensive review of all things welding certifications.
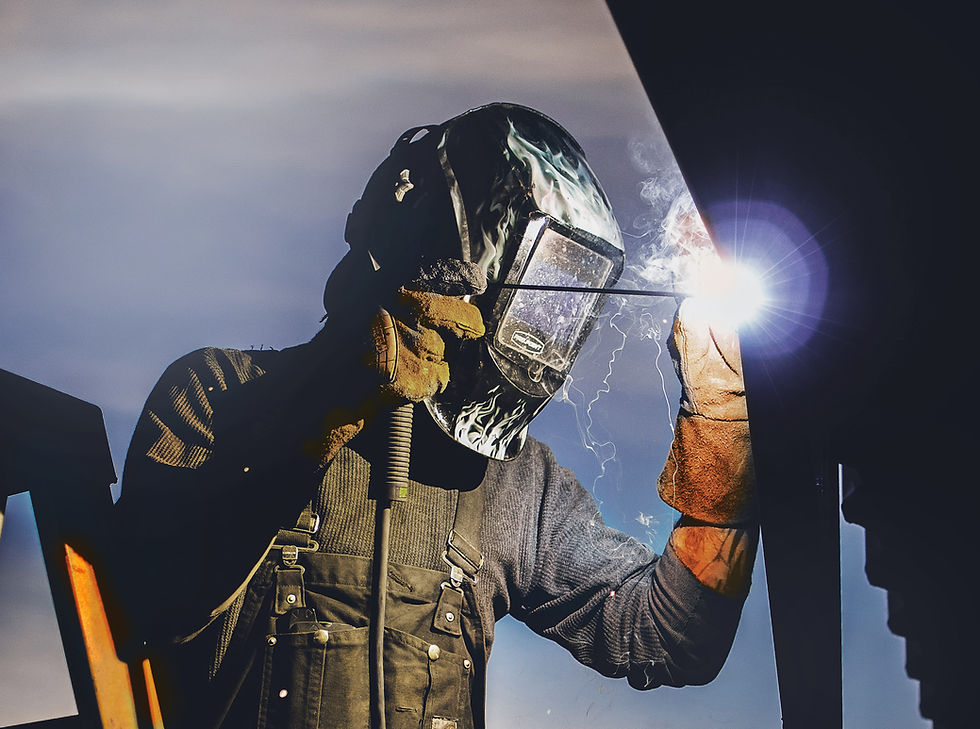
What Does "Certified Welder" Mean?
A certified welder is someone who has passed a test administered by a recognized certification body, such as the American Welding Society (AWS), demonstrating their ability to produce welds that meet certain standards. However, this certification can cover a wide range of welding processes, positions, and materials. Here are some key points to consider:
Certification by Specific Processes: A welder might be certified in one specific welding process, such as Shielded Metal Arc Welding (SMAW), Gas Tungsten Arc Welding (GTAW), or Flux-Cored Arc Welding (FCAW). Each process has its own set of skills and techniques, and being certified in one does not necessarily mean the welder is proficient in another.
Certification by Welding Positions: Welding certifications can also be position-specific. Common welding positions include flat, horizontal, vertical, and overhead. A welder certified for flat position welding may not be certified to weld in overhead or vertical positions, which require different techniques and skills.
Certification for Different Materials: Different materials, such as steel, stainless steel, or aluminum, require different welding techniques. A welder certified for welding carbon steel may not be qualified to weld stainless steel or aluminum without additional certification.
Certification for Joint Configurations: Welders may also be certified for specific joint configurations, such as butt joints, lap joints, T-joints, and corner joints. Each type of joint has unique characteristics and requires distinct welding techniques. A welder certified for a butt joint may not necessarily be certified for a T-joint based on the test that they were given.
Specificity is Important
When contacting a welding shop such as MFAB, it's essential to be specific about the type of certification you require for your project. Here are some tips to help you communicate your needs effectively:
Identify the Welding Process Required: Determine which welding process is best suited for your project. If you're unsure, consult with a welding professional who can help you identify the appropriate process based on the materials and requirements of your project.
Specify the Welding Positions: Make sure to specify the welding positions needed for your project. If your project requires welds in multiple positions, ensure that the welders are certified for all those positions.
Consider the Material: Clarify the type of material that needs to be welded. If your project involves multiple materials, verify that the welders have the necessary certifications for each material type.
Request Documentation: Ask for documentation of the welders' certifications. This should include the specific welding processes, positions, and materials they are certified to work with. Reputable welding shops will have no issue providing this information.

Prequalified Processes
Why Prequalified Processes Matter In the world of welding, prequalified processes are those that have been tested and proven to produce reliable welds without the need for additional qualification testing. These processes are outlined in standards like the AWS D1.1 Structural Welding Code, which details prequalified welding procedures for structural steel. Here’s why they extremely helpful and you should do your best to allow a fabricator to use pre-qualified processes as often as possible. 1. Streamlined Approval: Prequalified processes have already been vetted and approved by standards organizations (AWS), meaning they do not require further testing to verify their effectiveness. This can save time and resources in project planning and execution.
2. Cost-Effectiveness: By using prequalified processes, projects can avoid the costs associated with developing and testing new welding procedures. This can lead to significant savings, especially in large-scale projects where numerous welds are required.
3. Simplified Compliance: For many projects, especially those in industries like construction and manufacturing, adherence to recognized standards is mandatory. Prequalified processes ensure compliance with these standards, simplifying the approval process for project specifications and inspections.
Communicate your needs before the work is done.
Welding inspectors and Welding engineers look down on getting a welder certified after the work is performed and in some instances can even reject the work even if the welder retroactively passes the test and the work was acceptable. Before starting any project with MFAB you will be asked if your project requires any specific certifications beyond standard prequalified processes. If it does it is imperative that you inform us before starting so that we can get our staff appropriately certified before starting the work. As always, if you need help or have any questions feel free to reach out and we will do our best to help if we can.
-Charles